Whether you need hydroforming presses for high quantities, sinter presses with sophisticated control technology or nano presses with precise positioning, our experience in this area is very diverse, as the examples below show.
As a competent specialist with many years of experience, we offer you customized solutions that meet your requirements.
Your advantage at a glance:
- One contact for all questions
- Cost-effective solution
- Clear overall responsibility with one supplier
Fancy a few interesting application examples?
Application example 1: I(nternal) high pressure forming presses
In hydroforming presses, the water forms complex components with precise pressure control. In these machines, a pipe is filled with water, sealed and then formed using the deformation axes of the tool and a servo pressure intensifier. All process parameters can be optimized using the integrated oscilloscope. The pressure build-up curve can be used, for example, to make a statement about the product quality. This makes it possible to produce very complex components, for example for the automotive industry, in large quantities.
We have even designed and manufactured a complete machine for small components for one manufacturer. This machine has now produced several million parts, and a second machine was purchased to increase capacity.
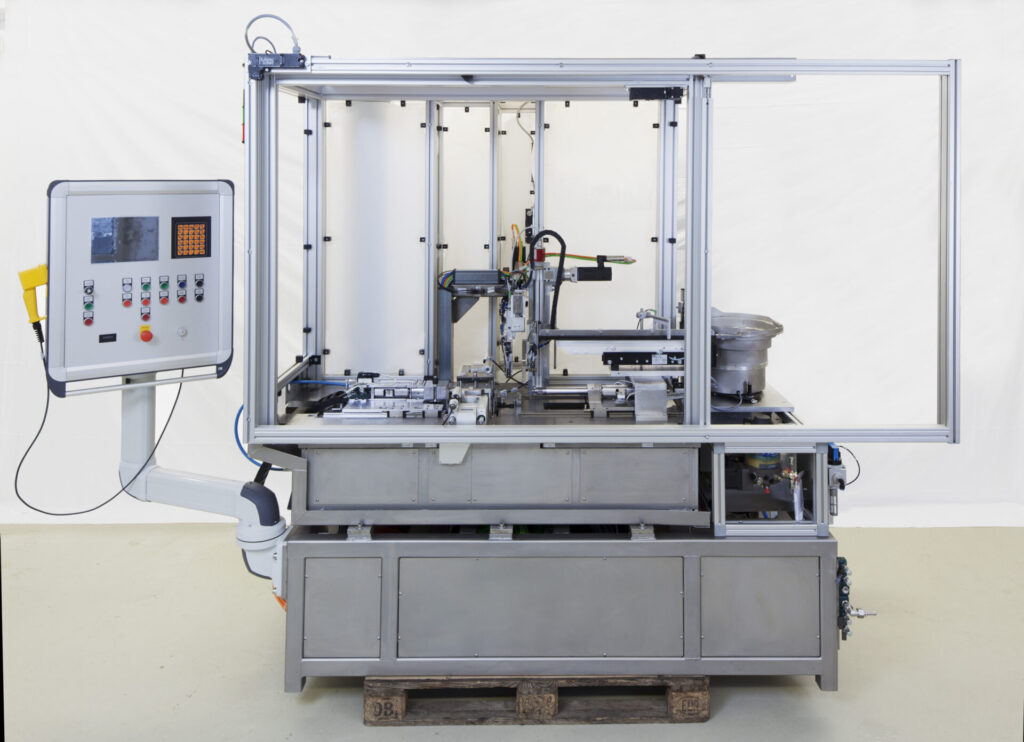
Application example 2: Sinter pressing
Sinter presses have a lower and an upper piston as their main axes, which are moved in relation to each other in a position and pressure-controlled manner. The high accuracy requirements demand special control functions. For example, a float-off function is required when filling the lower flask. To remove the parts that are still brittle, the upper piston must generate a gentle load so that the workpiece does not break at the edges when the lower piston is raised.
All these functions are implemented in our controller. In addition, there are various servo-hydraulic axes that have to be positioned depending on positions and cycle requirements. An example of this is the so-called filling shoe, which transports the sintering powder into the tool. We have stored various travel profiles and a fill level correction. This automatically modifies the filling quantity depending on the pressing result. This reduces the minimum deviations further and further.
All these axes are controlled centrally by the powerful CPU of our compact system with a cycle time of less than one millisecond. The system has a modular design and can control up to 16 axes. The measurement tolerance of the components is within 5µm. Hardware used: our compact system.
Application example 3: Test presses
These are used, for example, for pressure testing pipeline pipes that are 10 m long and 1.60 m in diameter. The test pressure is 160 bar. The sealing cylinder is pressure-controlled to prevent damage to the seal in the low-pressure range. Hardware used: our 19″ system.
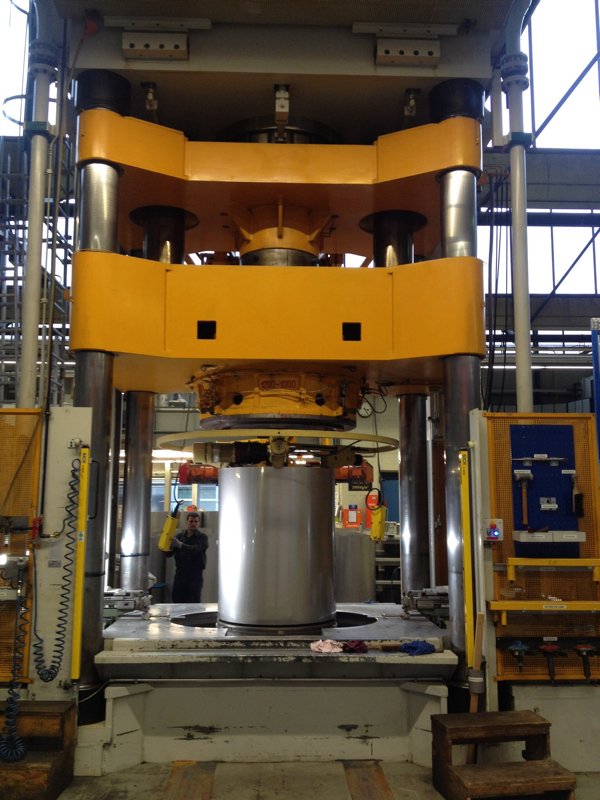
Application example 4: Plastic presses
This is a four-axis synchronous control system for the production of CFRP parts with undercut tools and special positioning steps for distributing the resin and pressure cycles to specifically influence the curing process. The control algorithm is based on the master-slave principle with a virtual master axis. Hardware used: our compact system.
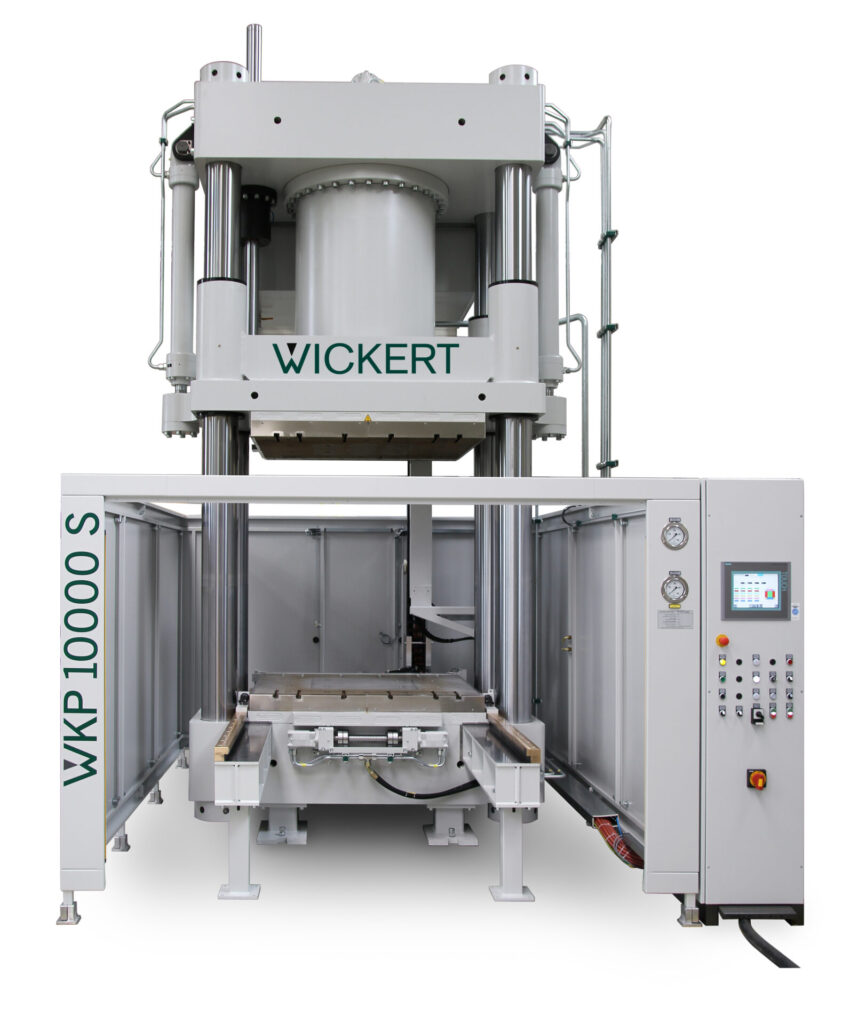
Application example 5: Tool tryout presses
We developed a two-axis synchronized control system for such a tool testing press. These presses are used for the development of stamping, drawing and injection molding tools and must guarantee precise pressing results, especially under eccentric loads. This is guaranteed by our ERM synchronization control module with dynamic monitoring and Profibus coupling. Hardware used: our ERM module.
Application example 6: Nanopressing
This process is used to emboss microstructures into a carrier material. The highlight of this application is the cylinder control, which has a minimum travel speed of 1µm/sec and a positioning accuracy of 0.1 µm.
The press is equipped with a vacuum unit. During embossing, all process parameters (pressure, position, temperature, etc.) are recorded online, displayed graphically and can be optimized. Hardware used: our compact system.
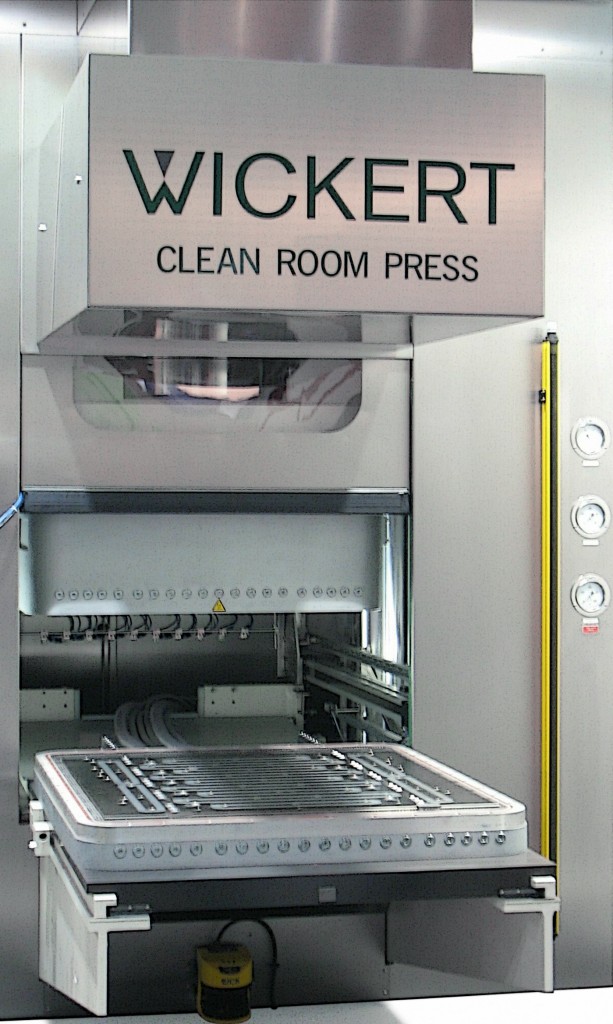