References
Pauly GmbH & Co KG Control and regulation systems

Our references
“How we use our innovative spirit, creativity and extensive experience to realize individual solutions for satisfied customers.”
In our more than 40 years of existence, customers worldwide have often confronted PSR with difficult tasks. Control and regulation challenges that had to be mastered – and which we solved to their satisfaction.
We are sure you will understand that the majority of our customers do not wish to be named. In order to not only tell you about our expertise and variety of solutions, but also to prove it, we have compiled a few examples from different areas.
Current case studies
Precision movement: So that Swiss watches move with the times – and not behind.
Requirement
The seconds accuracy of Swiss precision watches depends on how evenly thin a narrow stainless steel band has been rolled. For example, a supplier of Swiss precision mechanics requested a narrow strip with an output tolerance of max. a thousandth of a millimeter with a total thickness of 0.01 mm.
Solution
As the required rolling force was also relatively low (200kN), we designed a small servo-hydraulic cylinder with extremely low-friction seals and a dynamic servo valve (actuating time 0-100% 4ms) for this customer. Incremental encoders with a resolution of 0.05 µm were installed in the cylinder as a displacement measuring system.
Benefits and added value
The cylinders can be positioned with a reproducible accuracy of 0.1 µm.
Thickness control enables tolerances of ± 0.4 µm to be maintained precisely. Thanks to our precision roller setting system, customers can set the accuracy of their watches to the second and thus stay ahead of the competition!
Modernizing tried-and-tested products cost-effectively with comprehensive expertise
Requirement
After more than 40 years in continuous operation, a spring coiling machine with a base frame dating back to the 1960s required a general overhaul with functional enhancements. The aim was no longer to work with mechanical copying templates alone, but to digitize and save the product data and thus manufacture the springs in a reproducible manner.
Solution
We not only implemented a new control system according to the customer’s specifications, but also worked with them to develop a concept for converting the more than 150 mechanical copy templates into digital data. It goes without saying that the entire system was electrically overhauled, equipped in accordance with the latest safety guidelines and completely rewired. It is now state of the art and ready for the next 30 years of production.
Benefits and added value
Thanks to our comprehensive expertise in control systems, electrical systems and plant engineering, we were able to offer the customer the desired solution from a single source. The customer not only benefited from the cost-effective modernization of a proven machine, but also from time and cost savings thanks to a single competent solution provider.
Cost-effective modernization while ensuring the repeat accuracy of cylinder positioning in continuous operation
Requirement
As part of a machine modernization project, a hydraulic linear amplifier was to be replaced by a suitable servo valve. The customer had counting errors on the stepper motor controlling the linear amplifier and a recurring problem with the repeatable positioning of the cylinders (120/80 with 150 mm stroke; travel speed 120 mm/s; within 30 milliseconds with a tolerance of 1 / 100 mm).
Solution
Our investigations and simulations showed that a suitable servo valve would be very large, therefore expensive and also too slow for the required cycle time.
We replaced the stepper motor, which was no longer available, with a current make with improved performance data. In addition, a linear absolute scale (MTS with SSI interface) was attached to the linear cylinder to provide us with feedback on the actual cylinder position. This absolute signal was fed to a superimposed control loop, which ensures the required repeat accuracy of the positioning and monitors it redundantly.
Benefits and added value
Our customer thus benefited from a cost-effective solution while retaining the main hydraulic components and increasing positioning accuracy at the same time.
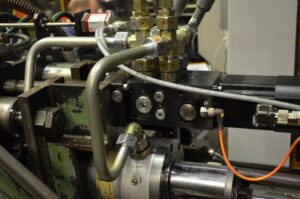
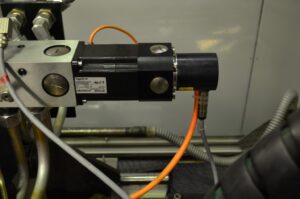
A quick solution for more precision – non-stop, so to speak
Requirement
Our customer needed a belt edge control system for his conveyor system. The old system he had installed was disturbed by incident sunlight and delivered poorly wound coils.
Solution
Together with him, we analyzed the problem and installed a new laser-based strip edge sensor and a new hydraulic control system with an additional absolute position sensor on the coiler. After a commissioning time of just three days (including electrical installation), the first coils were sold from the system.
Benefits and added value
The functioning components (hydraulics etc.) were retained and supplemented with new sensors, resulting in a cost-optimized system that solved the customer’s problem.
From conventional series machines to customized special designs
Requirement
High demands are also placed on compact machines. In itself, controlling a cutting machine is nothing complicated. This changes when a future-proof solution is required for a series machine in which several functions are to be combined on one circuit board.
The customer’s specifications included operation with a sophisticated graphical user interface (7″ multi-touch), the control of a 150 watt DC motor and the control of various pneumatic elements. Various interfaces (Ethernet and serial interfaces) were also required for communication and quality recording of the produced parts. With a cycle time of 400 milliseconds for the complete cutting cycle, the machine also runs quite quickly.
Solution
We developed a completely new hardware board for the customer with a Renesas RZ controller and its specified requirements; the software was created individually for the customer in the high-level language C.
The entire project was realized within 5 months, from the initial discussions to machine acceptance for series production.
Benefits and added value
Thanks to our electronics system, an integrated solution was created that combines all functions in a single unit – tailor-made for his series machine, which will be built in this way for the next ten years. The customer can thus build on our proven technologies in hardware and software and, thanks to our own electronics production, receives a future-proof solution that we can guarantee to supply for the next few years without any changes.
A side effect of this solution is that there are no additional software license costs for the series controllers, as the complete software, including the operating system, was created “in-house”.
Our customer was particularly impressed by the short power-on boot times of our control system; thanks to our own real-time operating system, the machine is ready for operation within one second.